As the hiring gap continues to widen, Deloitte and AWS are partnering up to bridge the divide through targeted and impactful digital training.
There’s an Indie video game called ‘Night In The Woods’ that exploded in popularity in 2018.
The game’s appeal, aside from its cute platform-style gameplay and colourful cast of animal characters, was its incredibly tangible, realistic storytelling.
So much of this storytelling came from its setting: the fictional town of Possum Springs, a contemplative rust-belt rendition of post-globalisation obsolescence.
There used to be work in the glass and tyre factory but opportunity dried up when manufacturers moved out or abroad, pursuing the desirable business incentives of setting up shop in China or India.
The world moved on, and it moved on without the workers in Possum Springs. In the real world today this dynamic has somewhat reversed.
We’ve all heard that the manufacturing sector has a hiring crisis, but it’s more than that. It’s a retention crisis, one that’s not just about retaining people but retaining vital knowledge.
- The World Economic Forum predicts a shortage of over 7 million skilled manufacturing workers by 2030
- According to McKinsey, a massive 87% of businesses report that they are either facing a skills shortage or expect to do so in the next five years
- Deloitte estimates that the skills gap could cost the US alone US$2.5tr over the next decade
- On top of this, up to 25% of the manufacturing workforce will retire in the next decade, draining decades of expertise
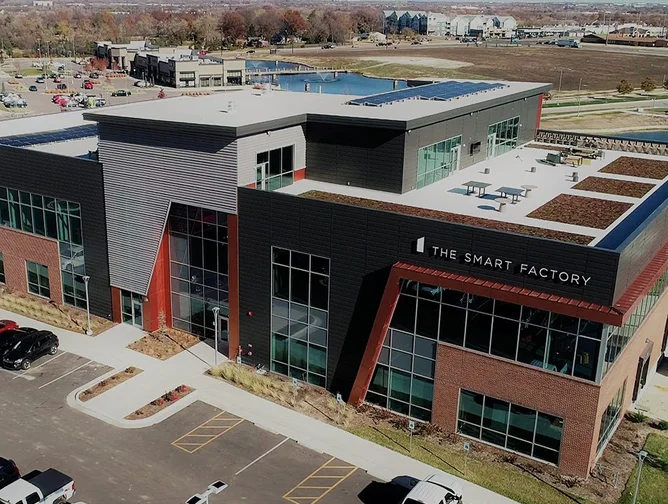
As technology rapidly advances and a wave of workers move on, who is going to take their place?
The scale of this problem has been recognised across the manufacturing sector, including by some of the most influential companies in the world.
“Roughly 112 million workers, 70% of the working population, hold frontline jobs,” says Francis Yu, Deloitte Unlimited Reality Business Lead, General Manager & Partner at Deloitte.
“These workers are the heart of every business, directly building and delivering products and serving customers and employees. Over 25% of the current manufacturing workforce is 55+ years old and on the cusp of retirement and they are not alone in a rapidly ageing workforce.
“At the same time, unplanned downtime due to operational or quality mishaps, increased concerns for worker safety, and increased complexity are all increasing the demand for innovation.”
Tim Gaus, Smart Manufacturing Business Leader at Deloitte agrees. “The skills gap is one of the biggest challenges for today’s manufacturers,” he says.
“In addition to upskilling/reskilling, manufacturing organisations are also faced with attracting the next generation of talent among stereotypes of manufacturing plants and jobs of yesteryears.
“Changing this perception to attract those new to the workforce will require investment and creative use of advanced technology like metaverse, AI, and more.”
These technologies – the key to attracting this new wave of talent – will also need to address the knowledge the manufacturing industry will lose due to what many call the ‘silver tsunami’.
“The tribal knowledge of these workers leaves with them unless you can digitally capture their insights and daily work operations,” says Douglas Bellin, Worldwide Head of Smart Manufacturing at Amazon Web Services.
The retirement wave is creating a more inexperienced workforce, according to Doug, with new workers needing guidance on how to improve quality, output and other key facility metrics that previous generations didn’t.
That intuitive knowledge, refined by decades of experience, is now fatally missing.
Deloitte and Amazon Web Services have come together to tackle this dilemma, bringing together Deloitte’s Unlimited Reality™ practice and Amazon Q for Business.
Unlimited training through Gen AI, AR and VR
“Deloitte’s Unlimited Reality™ practice helps our clients engage with the enterprise and industrial metaverse with confidence, intention, and integrity,” says Frances Yu.
“Our multidisciplinary practice brings together comprehensive capabilities, including design, AI/ML expertise, engineering, and business strategy. Our goal is to help our clients experience the benefits of the next wave of digital transformation.”
In collaboration with Amazon, Deloitte has created an end-to-end frontline worker solution integrated with generative AI (Gen AI) that leverages AR for on-the-job upskilling and intelligent assistance.
Deloitte Unlimited Reality integrates the vast capabilities required to deliver spatial solutions – from reality capture and multimodal data storage to 3D design and engineering.
“Our solution helps clarify complex procedures with a step-by-step AR work instruction experience, featuring 3D models of machinery and a custom generative AI solution,” Frances says.
By providing real-time insights within the regular workflow, this training method decreases
downtime and triage service requests and provides superior visibility into asset health and performance.
This method also disrupts the typical siloing of enterprise data, making it immediately accessible to frontline workers and thus enhancing the efficiency and safety of their work.
Not only does the 3D training of frontline workers boast superior results, but it also boasts superior flexibility. New employees and established experts can coordinate and collaborate from completely different locations, creating an enhanced learning experience.
“Their physical realities are each overlayed with a digital component, and they can work with different solutions by running simulations in real-time,” says Tim.
Frances agrees, noting that, unlike traditional training methods, workers can learn without being taken away from frontline duties, avoiding unnecessary downtime.
“3D training enables ‘learning by doing’ for frontline workers and results in faster problem solving, fewer errors and, most importantly, helps a critical population of workers to thrive on the job,” she explains.
Digital twins, AR and Gen AI are also utilised within training to make work safer, through predictive maintenance flagging and safe employee introductions to new high-risk machinery, systems and processes. With Gen AI, closed-loop manufacturing systems can be created that automatically make real-time adjustments and self-optimise based on data.
Amazon Q for Business, an integral part of Deloitte’s Unlimited Reality practice, is a Gen AI-powered assistant for enterprises that enables employees to receive comprehensive answers to complex questions in a quick, conversational manner.
“Generative AI is in the early stages both in the market and as a technology,” Doug notes.
“The key that I see to make Gen AI a success is the data; ensuring data quality and governance are built upon and followed to allow the technology to be used.”
According to Doug, the first use cases involved dissecting information from reports, and altering bar charts to pie charts without additional programming until they evolved into using natural language to obtain answers. The transition has been gradual, following AWS’ established approach.
“At AWS we say ‘crawl, walk, run.’ For example, a single use case to solve could be the crawling stage, where many people start, but a large percentage stall – often referred to as pilot purgatory,” says Doug.
Doug says that in order to scale programmes from the start businesses need to implement the correct technology and define specific data to move from crawling to walking and out of pilot purgatory.
“Working with companies that have gone through this and built with scale as a goal will help you succeed and accelerate your journey.”
Now AWS’ journey involves working with Deloitte to help manufacturers tackle training in the era of Industry 4.0.
“We’ve created a solution that supports workers in industrial settings, which often needs to be hands-free, as well as elevating the training experience to improve productivity and cost efficiency by providing context-aware intelligent assistance,” Doug explains.
“Could a worker in the future walk up to a machine and ask ‘how are you running today’ and receive back an answer on its status, its health and potential time to possible failure and what parts it needs to stay healthy?”
These questions reflect the endless potential of these technologies, a sentiment with which Tim agrees.
“This innovation is a great example of how the convergence of technologies is opening doors to capabilities that augment work and productivity,” he says.
“Keeping the human worker at the centre of this innovation is paramount. Let technologies like Gen AI and spatial computing enhance what humans can do, democratising the value of technology and empowering workers to expand their skills and therefore expand the value offered by the enterprise.”
Deloitte & AWS: a powerful alliance
Deloitte and AWS are long-time collaborators, with a powerful alliance that spans a decade. Deloitte is a Premier Tier Partner in the AWS Partner Network and has invested in shared capabilities including 80 industry-specific solutions and tools co-created from the ground up.
AWS, meanwhile, is a founding member of The Smart Factory by Deloitte at Wichita. The facility has a working production line where STEM kits are produced for underprivileged youth to give them real-world building experience.
Doug says here customers are brought here to be shown the “art of the possible.” With the looming scale of the retention crisis, being open to this art will be vital for manufacturers.
People are moving on and the world continues to change, as swift and indifferent as the winds.
Manufacturers must adapt or they’ll be getting left behind – just like Possum Springs.